For tiden har de ledende hærene i verden begynt å implementere programmer for utvikling av nye typer håndvåpen (Ratnik i Russland og NGSAR i USA). Som mer enn et århundre erfaring med utvikling av enhetspatroner, og deretter mellomliggende og lavimpulspatroner, viser, er den mest lovende løsningen den avanserte utviklingen av nye typer ammunisjon.
Etter resultatene av andre verdenskrig ble det konkludert med at det var nødvendig å forbedre utformingen av den mest forbrukbare ammunisjonstypen (patroner for automatiske håndvåpen) og utvide ressursbasen for produksjonen.
Patroner med metallhylser
Metningen av infanterienheter med automatvåpen i forsvarsindustrien har forårsaket mangel på kobber, tradisjonelt brukt i patronmessing (brukt til å lage patronhylstre) og tompak (brukt til å lage kulehylstre).
Den mest effektive løsningen på problemet med ressursknapphet var bruk av mildt stål, belagt på begge sider med kobber for korrosjonsbeskyttelse, eller ubelagt, brukt i krigstid for produksjon av såkalte surrogatforinger. I etterkrigstiden ble teknologien for å belegge stålhylser med en spesiell lakk mestret, som beskyttet dem mot fuktighet og redusert friksjon i kammeret (opp til en viss temperaturgrense).
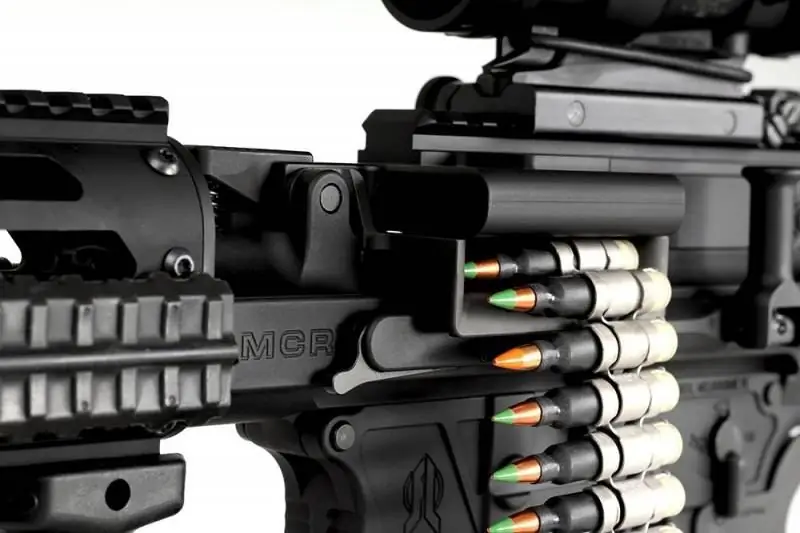
Til tross for de lignende tekniske egenskapene til mildt stål og kobberlegeringer, har sistnevnte fordeler i formbarhet og korrosjonsbestandighet. Lakkbelegget av stålhylser har lav slitestyrke og har en tendens til å bli skadet og overført til automatiseringselementene ved å laste det på nytt med metalldeler av våpenet. Hvis ubrukte patroner fjernes fra fatet etter avslutning av avfyring, fratas dekslene på lakkbelegget på grunn av utbrenthet ved kontakt med den oppvarmede overflaten av kammeret, hvoretter de akselereres og oksyderes og patronene blir uegnet for videre bruk.
Det økte forbruket av patroner av infanterister bevæpnet med automatvåpen tjente som grunnlag for en økning i bærbar ammunisjon ved å redusere vekten av patroner. Fram til begynnelsen av 1970-tallet var hovedretningen for å redusere vekten på den ammunisjonen som var på bruk, overgangen først til mellomliggende, og deretter til lavimpulspatroner, på grunn av ønsket om å øke nøyaktigheten av automatisk brann fra vanskelige posisjoner. Etter adopsjonen av AK-74-angrepsgeværet og automatgeværet M-16, ble denne reserven for å redusere vekten på den ammunisjonen som ble brukt, oppbrukt-et forsøk på å bruke lettere feide kuler avslørte deres økte vinddrift.
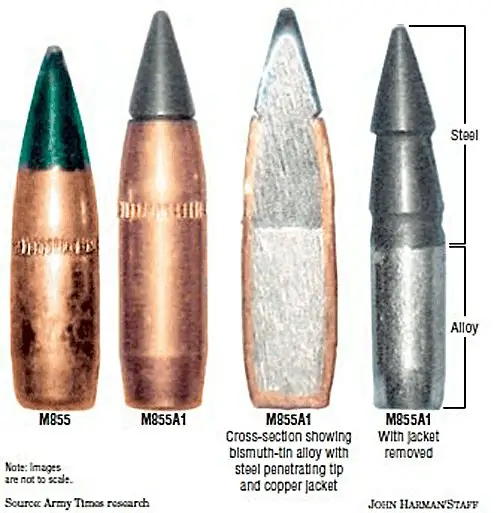
For tiden brukes kuler med stålkjerne, blyjakke og tompakjakke hovedsakelig som slående elementer. For å øke rustningspenetrasjonen gikk den amerikanske hæren over til bruk av kuler av metall av M80A1 EPR og M855A1 patroner uten blyjakke, bestående av et tombakskall og en kjerne med stålhode og vismuthale.
Kasseløse patroner
På 1980 -tallet, i Sovjetunionen og NATO -landene, ble det forsøkt radikalt å løse problemene med det høye materialforbruket til klassiske patroner ved å bytte til saksløs ammunisjon. Den største fremgangen i denne retningen ble oppnådd av det tyske selskapet Heckler und Koch, som opprettet HK G11 automatgevær, som brukte de sakløse DM11 -kassettene utviklet av Dynamit Nobel.
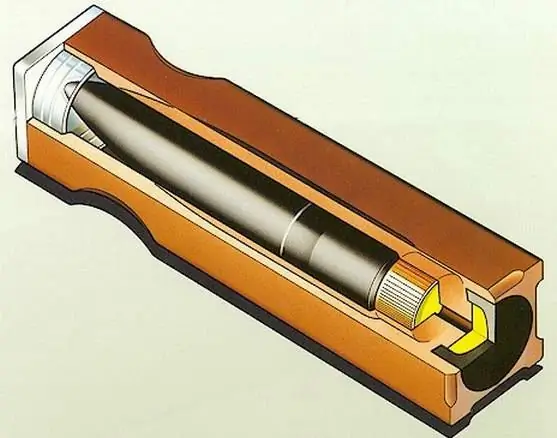
Imidlertid demonstrerte den militære operasjonen av en serie på 1000 HK G11 -rifler i FRG -grensetjenesten deres fare for militært personell på grunn av den regelmessige spontane forbrenningen av kasseløse patroner i kammeret, til tross for den strukturelle separasjonen fra geværløpet. Som et resultat ble de tyske grensevaktene først utestengt fra å bruke den automatiske avfyringsmodusen, og deretter ble HK G11 helt tatt ut av drift på grunn av meningsløsheten ved bruk som et rent selvlastende våpen i nærvær av overkomplisert automatisering (" gjøkur").
Patroner med plasthylser
Det neste forsøket på å redusere materialforbruket til håndvåpen ammunisjon og øke bærbar ammunisjon ble utført på 2000 -tallet i USA av AAI (nå Textron Systems, en produksjonsavdeling av Textron Corporation) som en del av LSAT (Lightweight Small Arms Technologies)) -programmet, som førte til opprettelsen av et lett maskingevær og en automatisk karbin, designet for kombinert ammunisjon med patroner med en messinghylse, en plasthylse og caseless, laget i en teleskopisk formfaktor.
Kasseløse patroner ble som forventet notert for spontan forbrenning i fatkammeret, til tross for den avtakbare utformingen, så valget i LSAT -programmet ble gjort til fordel for patroner med plasthylse. Ønsket om å redusere kostnaden for ammunisjon førte imidlertid til feil valg av plasttype: polyamid ble brukt som sådan, som har alle nødvendige egenskaper, bortsett fra en, men den viktigste - den maksimale driftstemperaturen overstiger ikke 250 grader Celsius.
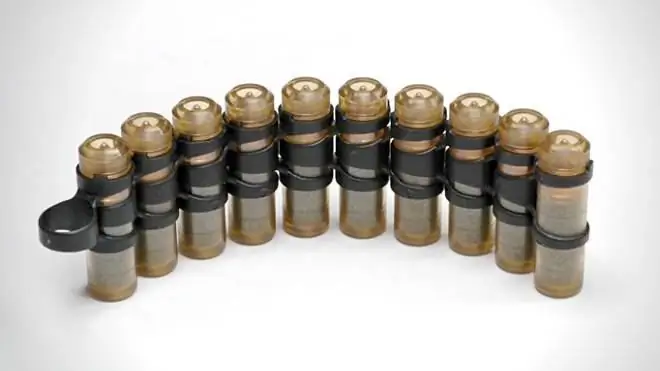
På 1950 -tallet ble det på grunnlag av resultatene fra felttester fastslått at fatet til en DP -maskingevær under kontinuerlig avfyring i utbrudd med pauser for skiftende butikker varmer opp til følgende verdier:
150 skudd - 210 ° C
200 skudd - 360 ° C
300 skudd - 440 ° C
400 skudd - 520 ° C
Med andre ord, under intens kamp, etter å ha brukt de første to hundre patronrundene, vil fatet til et lett maskingevær garantert nå smeltepunktet for polyamid.
I forbindelse med denne omstendigheten ble LSAT -programmet avsluttet i 2016, og på grunnlag av dette ble CTSAS (Cased Telescoped Small Arms Systems) -programmet lansert med sikte på å utvikle teleskopkassetter på nytt materialbasis. I følge et intervju med US Army Program Administrator Corey Phillips gitt til thefirearmblog.com i mars 2017, er den hittil mest varmebestandige ingeniørpolymeren, polyimid, valgt for plasthylse-materialet, med en maksimal driftstemperatur på 400 ° C.
Polyimid som materiale i patronhylsteret har også en annen verdifull egenskap - når det varmes opp over det angitte nivået, forkulles det uten å smelte med frigjøring av flyktige stoffer som ikke forurenser fatkammeret, mens den forkullede overflaten på kassetthuset fungerer som en utmerket antifriksjonsmateriale når det trekkes ut etter et skudd. Styrken på foringsfelgen er gitt av en metallflens.
En temperatur på 400 grader er den tillatte grensen for oppvarming av håndvåpenfat, hvoretter de blir vridd, siden temperaturen på den teknologiske tempereringen av fatene er fra 415 til 430 grader. Imidlertid faller strekkfastheten til polyimid ved temperaturer på 300 grader eller mer til 30 MPa, noe som tilsvarer et kammertrykk på 300 atmosfærer, dvs. en størrelsesorden mindre enn det maksimale trykket i pulvergasser i moderne modeller av håndvåpen. Når det blir forsøkt å fjerne en brukt patronhylster fra kammeret i klassisk design, vil metallflensen rive av med en ramrod som slår ut restene av patronhuset fra fatet.
Oppvarmingen av patronen i kammeret i den klassiske designen kan til en viss grad styres ved å skyte fra en åpen bolt (maskingevær), men ved intens avfyring og avfyring fra en lukket bolt (maskingevær og automatgeværer), oppvarming av patronen over 400 grader er nesten uunngåelig.
Patroner med aluminiumshylser
Et annet alternativ til kobberlegeringer er aluminiumlegeringer, som brukes i foringsrørene til serielle pistolkassetter, i eksperimentell utvikling av riflepatroner og i seriebilder for den 30 mm automatiske kanonen GAU-8A. Ved å erstatte kobber med aluminium kan du fjerne begrensningen på ressursbasen, redusere kostnaden for patronhylsen, redusere vekten på ammunisjonen med 25 prosent og følgelig øke den bærbare ammunisjonsbelastningen.
I 1962 utviklet TsNIITOCHMASH eksperimentelle patroner av 7, 62x39 mm kaliber med en aluminiumslegeringshylse (kode GA). Foringene hadde et antifriksjonsgrafitbelegg. For å forhindre elektrokjemisk korrosjon, var kapselkoppen laget av en aluminiumslegering.
Imidlertid hindres bruken av slike hylser av deres eneste negative egenskap - spontan antennelse av aluminium og dets legeringer i luft ved oppvarming til 430 ° C. Forbrenningsvarmen til aluminium er veldig høy og utgjør 30,8 MJ / kg. Produktets ytre overflate utsettes for spontan forbrenning ved oppvarming til en spesifisert temperatur og en økning i permeabiliteten til oksydfilmen for oksygen i luften eller ved oppvarming til en lavere temperatur ved skade på oksydfilmen. En ikke -plastisk keramisk oksidfilm (tykkelse ~ 0,005 mikron) ødelegges når en metallhylse av plast deformeres under påvirkning av trykket av drivgasser, og permeabiliteten til oksydfilmen oppnås som et resultat av oppvarming under intens avfyring. Liners antennes spontant bare i luft etter ekstraksjon fra fatet, hvor en negativ oksygenbalanse opprettholdes under forbrenningen av pulveret.
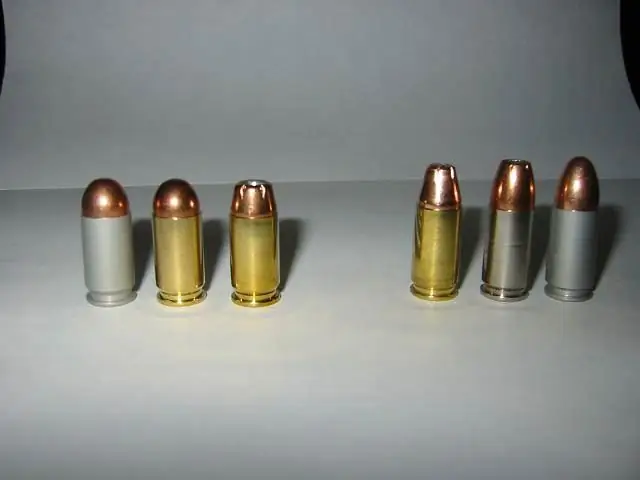
Derfor har aluminiumshus blitt utbredt bare som en del av pistolkassetter med kaliber 9x18 PM og 9x19 Para, hvis intensitet av ild og temperaturen som er nådd i kammeret, kan ikke sammenlignes med disse indikatorene for maskingevær, automatiske rifler og maskingevær.
Aluminium ble også brukt i den eksperimentelle 6x45 SAW Long -kassetten, hvis hylse var utstyrt med en elastisk silikonforing som strammer sprekker i metall- og oksidfilmen. Imidlertid førte denne beslutningen til en økning i patronens lineære dimensjoner, mottakerens tilhørende dimensjoner og følgelig vekten av våpenet.
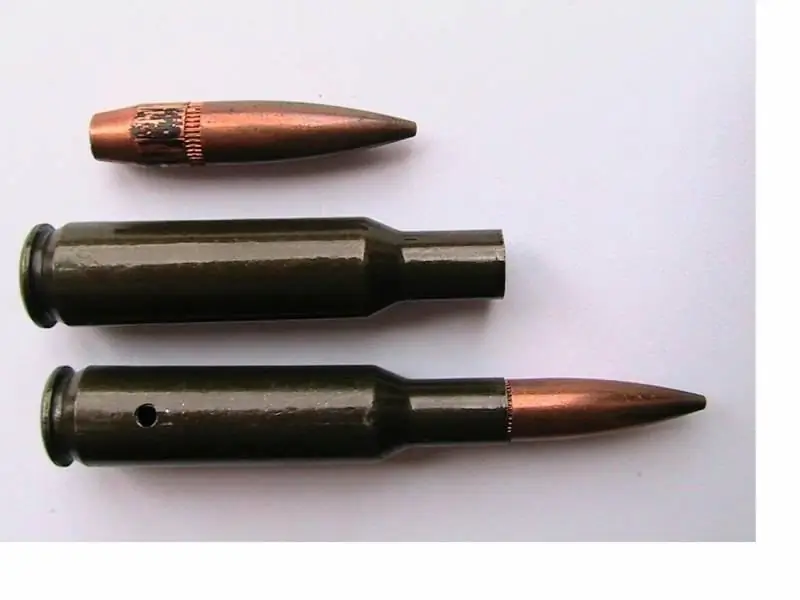
En annen løsning, men tatt i bruk, er 30x173 GAU artillerirunden med en aluminiumslegeringshylse. Dette ble mulig på grunn av bruk av en spesiell lavmolekylær "kald" drivstoffladning. Det termokjemiske potensialet til pulveret er direkte proporsjonalt med forbrenningstemperaturen og omvendt proporsjonalt med molekylvekten til forbrenningsproduktene. Klassiske nitrocellulose- og pyroksyliniske drivmidler har en molekylvekt på 25 og en forbrenningstemperatur på 3000-3500 K, og molekylvekten til det nye drivstoffet var 17 ved en forbrenningstemperatur på 2000-2400 K ved samme impuls.
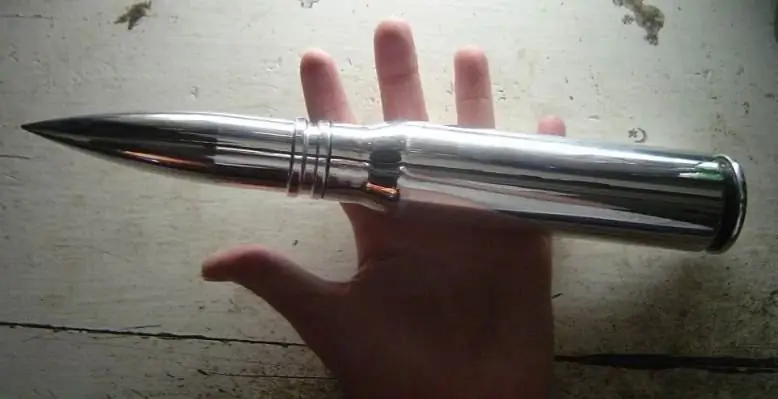
Lovende sintret metallhylse
Den positive opplevelsen av å bruke artilleriskudd med aluminiumshylse gjør det mulig å betrakte dette metallet som et konstruksjonsmateriale for patronvesker for håndvåpen (selv uten en spesiell drivstoffkomposisjon). For å bekrefte riktigheten av det angitte valget, er det tilrådelig å sammenligne egenskapene til messing- og aluminiumslegeringsforinger.
Messing L68 inneholder 68 prosent kobber og 32 prosent sink. Dens tetthet er 8,5 g / cm3, hardhet - 150 MPa, strekkfasthet ved 20 ° C - 400 MPa, strekkforlengelse - 50 prosent, glidende friksjonskoeffisient på stål - 0,18, smeltepunkt - 938 ° C, temperatursone for sprøhet - fra 300 til 700 ° C.
Som erstatning for messing foreslås det å bruke aluminium legert med magnesium, nikkel og andre kjemiske elementer i en volumfraksjon på ikke mer enn 3% for å øke de elastiske, termiske og støpende egenskapene uten å påvirke legeringens motstand mot korrosjon og sprekker under belastning. Legeringens styrke oppnås ved å forsterke den med dispergerte aluminiumoksydfibre (diameter ~ 1 mikrometer) i en volumfraksjon på 20%. Beskyttelse mot selvantennelse på overflaten gis ved å erstatte den sprø oksidfilmen med et plastbelegg av kobber / messing (~ 5 mikrometer tykt) påført ved elektrolyse.
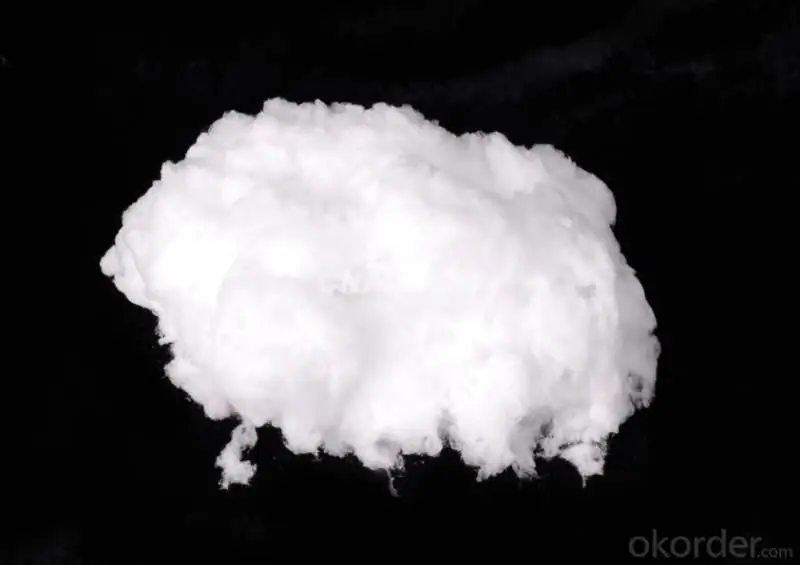
Den resulterende cermet -kompositten tilhører klassen av cermets og formes til et sluttprodukt ved sprøytestøping for å orientere forsterkningsfibrene langs foringsaksen. Anisotropien til styrkeegenskapene gjør det mulig å bevare komposittmaterialets samsvar i radial retning for å sikre tett kontakt mellom hylseveggene og kammeroverflaten under påvirkning av trykket i pulvergassene for å tette sistnevnte.
Antifriksjons- og gripegenskapene til foringen sikres ved å påføre et polyimid-grafittbelegg (tykkelse ~ 10 mikron) på ytre overflate med like volumfraksjoner av bindemiddel og fyllstoff som tåler en kontaktbelastning på 1 GPa og en driftstemperatur på 400 ° C, brukt som belegg for forbrenningsmotorstempler.
Tettheten til cermet er 3,2 g / cm3, strekkfasthet i aksial retning: ved 20 ° C - 1250 MPa, ved 400 ° C - 410 MPa, strekkfasthet i radial retning: ved 20 ° C - 210 MPa, ved 400 ° C - 70 MPa, strekkforlengelse i aksial retning: ved 20 ° C - 1,5%, ved 400 ° C - 3%, strekkforlengelse i radial retning: ved 20 ° C - 25%, ved 400 ° C - 60 %, smeltepunkt - 1100 ° C.
Glidefriksjonskoeffisienten til antifriksjonsbelegget på stål er 0,05 ved en kontaktbelastning på 30 MPa og over.
Den teknologiske prosessen for produksjon av kermethylser består av færre operasjoner (blanding av metall med fiber, støping av hylser, varm rifling av felg og boring, messing, påføring av et antifriksjonsbelegg) sammenlignet med antall operasjoner i teknologisk prosess for fremstilling av messinghylser (støping av billets, kaldtegning i seks passasjer, kald rifling av felg og nakke).
Vekten på messinghylsen til patronen 5, 56x45 mm er 5 gram, vekten på cermet -ermet er 2 gram. Prisen på ett gram kobber er 0,7 amerikanske cent, aluminium - 0,2 amerikanske cent, kostnaden for dispergerte alumina -fibre er 1,6 amerikanske cent, vekten i foringen overstiger ikke 0,4 gram.
Lovende kule
I forbindelse med adopsjonen av hærens rustningsklasse 6B45-1 og ESAPI, ikke penetrert av kuler av håndholdte håndvåpen med en stålkjerne i en avstand på 10 meter eller mer, er det planlagt å gå over til bruk av kuler med en sintret legeringskjerne av wolframkarbid (95%) og koboltpulver (5%) med en egenvekt på 15 g / cm3, som ikke krever vekting med bly eller vismut.
Hovedmaterialet i kulene er en tombak, bestående av 90% kobber og 10% sink, hvis tetthet er 8,8 g / cc, smeltepunktet er 950 ° C, strekkfastheten er 440 MPa, den kompresjonsmessige styrke er 520 MPa. hardhet - 145 MPa, relativ forlengelse - 3% og friksjonskoeffisient på stål - 0,44.
På grunn av økningen i starthastigheten til kuler til 1000 og flere meter per sekund og en økning i brannhastigheten til 2000 og flere runder per minutt (AN-94 og HK G-11), oppfyller tombakken ikke lenger kravene for kuleskall på grunn av høy termoplastisk slitasjehull på grunn av høy glidekoeffisient for kobberlegering på stål. På den annen side er artilleriskjell kjent, i utformingen av hvilke de kobberledende beltene erstattes av plast (polyester), hvis friksjonskoeffisient er på nivået 0, 1. Imidlertid er driftstemperaturen til plasten belter overstiger ikke 200 ° C, som er halvparten av maksimumstemperaturen på håndvåpenfat opp til begynnelsen av vridningen.
Derfor, som et skall av en lovende kule med en helt metallkjerne, foreslås det å bruke en polymerkompositt (tykkelse ~ 0,5 mm) som inneholder polyimid av typen PM-69 i like volumfraksjoner og kolloidal grafitt med en total tetthet på 1,5 g / cc, strekkfasthet 90 MPa, trykkfasthet 230 MPa, hardhet 330 MPa, kontaktbelastning 350 MPa, maksimal driftstemperatur 400 ° C og glidende friksjonskoeffisient på stål 0,05.
Skallet dannes ved å blande polyimidoligomeren og grafittpartiklene, ekstrudere blandingen i en form med en innebygd del - kulekjernen og temperaturpolymerisering av blandingen. Vedheftet av skallet og kulekjernen sikres ved at polyimid trenger inn i kjernens porøse overflate under påvirkning av trykk og temperatur.
Lovende teleskopkassett
For tiden anses den mest progressive formfaktoren for en håndvåpenkassett å være teleskopisk med plassering av en kule inne i en presset drivgass. Bruken av en tett brikke i stedet for den klassiske kornladningen med lavere bulkdensitet gjør det mulig å redusere lengden på patronen og de tilhørende dimensjonene til våpenets mottaker med opptil en og en halv gang.
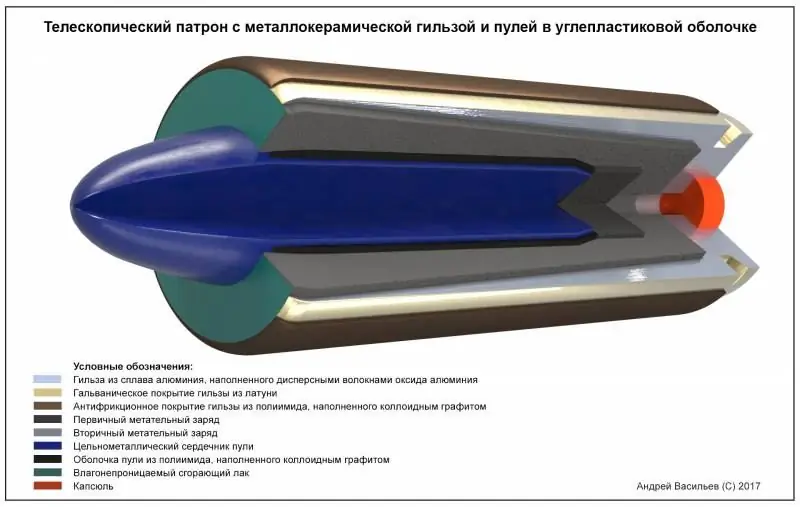
På grunn av utformingen av lastemekanismen (avtagbart fatkammer) på håndvåpenmodeller (G11 og LSAT) ved bruk av teleskopkassetter, er kulene deres fordypet i drivbrikkene under kantene på ermet. Den åpne enden av den sekundære drivstoffladningen fra smuss og fuktighet beskytter en plasthette, som samtidig fungerer som en foran obturator ved avfyring (ved å blokkere skjøten mellom det avtakbare kammeret og fatet etter et kulegjennombrudd). Som praksisen med militær operasjon av teleskopkassetter DM11 har vist, fører en slik metode for montering av patronen, som ikke gir vekt på kulen i kulens inngang til fatet, til forvrengning av kulen når den avfyres, og følgelig tap av nøyaktighet.
For å sikre den spesifiserte driftssekvensen til den teleskopiske patronen, er drivstoffladningen delt i to deler - en primærladning med relativt lav tetthet (med en høyere forbrenningshastighet), som ligger direkte mellom kapselen og bunnen av kulen, og en Tirsdag ladning av relativt høyere tetthet (med lavere brenningshastighet), lokalisert konsentrisk rundt kulen. Etter at primeren er gjennomboret, utløses primærladningen først, skyver kulen inn i boringen og skaper et boosttrykk for den sekundære ladningen, som beveger kulen i boringen.
For å beholde kontrollen av den sekundære ladningen inne i kassetten, er kantene på den åpne enden av hylsen delvis rullet opp. Beholdelsen av kulen i patronen utføres ved å trykke den inn i blokken av den sekundære ladningen. Å plassere en kule langs hele lengden i hylsens dimensjoner reduserer kassettlengden, men skaper samtidig et tomt volum av hylsen rundt den ogival delen av kulen, noe som fører til en økning i diameteren på patron.
For å eliminere disse manglene, foreslås en ny layout av teleskopkassetten, beregnet for bruk i håndvåpen med et klassisk integrert fatkammer med alle typer lastemekanismer (manuell, gassmotor, bevegelig tønne, halvfritt breechblock, etc..) og en metode for avfyring (med sear foran eller bak).
Den foreslåtte patronen er utstyrt med en kule som strekker seg ogival -delen utover ermet og på grunn av dette støter mot kulens innløp i fatet. I stedet for en plasthette, er den åpne enden av drivstoffladningen beskyttet av en fuktresistent lakk som brenner ut ved avfyring. En viss økning i lengden på den foreslåtte patronen sammenlignet med de kjente teleskopkassettene kompenseres av en reduksjon i dens diameter på grunn av eliminering av ufylte volumer inne i hylsen.
Generelt vil den foreslåtte teleskopkassetten øke antall patroner i infanteristens bærbare ammunisjon med en fjerdedel, samt redusere materialforbruket, arbeidsintensiteten og produksjonskostnadene for patronhylser.