Krig er kjent for å være den beste fremdriftsmotoren. Tankindustrien i Sovjetunionen gjorde et svimlende kvalitativt sprang på bare noen få krigsår. Den sanne kronen til dette var tankene i IS -serien.
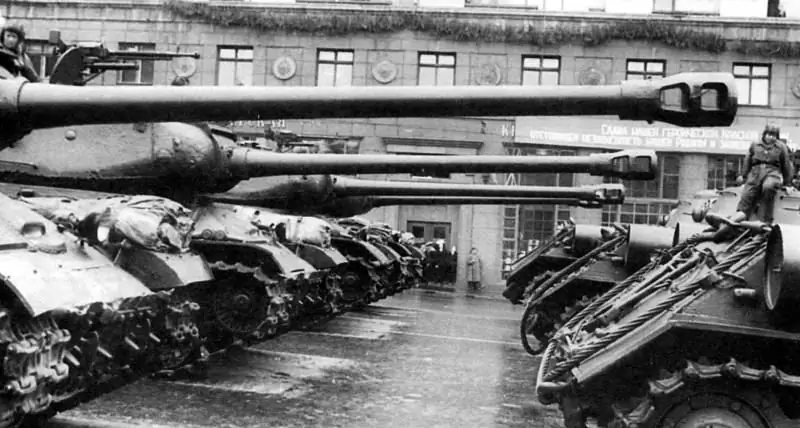
Magnitogorsk oppskrifter
I forrige del av historien handlet det om 70L støpt rustning med høy hardhet som ble brukt til tårnene til IS-tankene. Panserutviklerne fra TsNII-48 var langt fra den første erfaringen med å skape beskyttelse for tunge stridsvogner.
Før Kursk Bulge, som ble en katalysator for utviklingen av innenlandske tunge tankbygg, var hovedformålet med moderniseringen KV -tanken. I utgangspunktet var alt arbeid rettet mot å redusere andelen knappe legeringsadditiver i rustningens sammensetning. Selv navnet i TsNII -48 kom med et passende navn - økonomisk legert stål. Den originale rustningen til merkevaren FD-7954, som KV-tanken gikk inn i den store patriotiske krigen, inneholdt, i henhold til tekniske krav, opptil 0,45% molybden, 2,7% nikkel og krom.
I slutten av 1941 opprettet en gruppe forskere ledet av Andrei Sergejevitsj Zavyalov ved det pansrede instituttet en oppskrift på stål FD -6633 eller 49C, der molybden ikke krevde mer enn 0,3%, krom - opptil 2,3%og nikkel - opptil 1, 5%. Med tanke på at tankene i KV -serien fra andre halvdel av 1941 til 1943 ble samlet om lag 4 tusen eksemplarer, kan man forestille seg mengden reelle besparelser i legeringsmetaller.
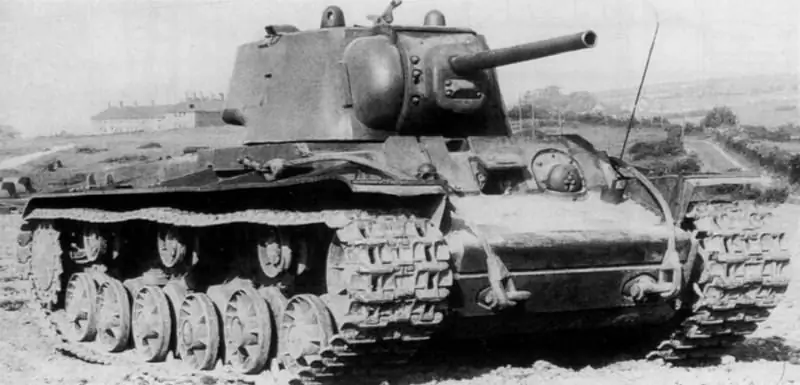
Hemmeligheten til suksess
Hemmeligheten bak metallurgens suksess ligger i studiet av parametrene for dannelsen av fibrøst brudd i rustning - hovedparameteren for prosjektilmotstand. Det viste seg at du kan klare deg uten en betydelig andel legeringselementer ved å endre kjølehastigheten til rustningen under slukking. Men dette er enkelt i ord - hvor mange foreløpige eksperimenter og smelter metallurgene måtte gjøre, vil bare de nå klassifiserte arkivene kunne fortelle.
På Magnitogorsk Metallurgical Plant i 1941 ble de første prototypene av 49C stål oppnådd, som ikke var dårligere enn den tradisjonelle "førkrig" rustningen. Spesielt viste beskytningen av 76 mm kanonen full overensstemmelse med de taktiske kravene til tanken. Og siden 1942 ble bare rustning med navnet 49C brukt til KV -serien. Det er verdt å huske at forbruket av krom, molybden og nikkel har redusert betydelig.
Søket etter nye rustninger for tungt utstyr endte ikke der. I 1942 ble stål GD-63-3 "sveiset", helt blottet for knappt krom og nikkel. Til en viss grad ble nikkel erstattet av mangan - andelen økte mer enn tre ganger (opptil 1,43%). Prototyper av den nye rustningen ble avfyrt. Og de viste seg å være ganske egnet for massebruk i utformingen av KV. Men Klim Voroshilov -stridsvognene med rustning av middels hardhet trakk seg. Og stedet for tunge kjøretøyer ble tatt av "Joseph Stalin" -kjøretøyer med rustning med høy hardhet.
Valset rustning 51C
Hvis 70L-rustningen til IS-2-tårnet kunne støpes, fungerte ikke dette trikset med tankens skrogdeler. Her sto ingeniører overfor to problemer samtidig - opprettelsen av rustninger med høy hardhet med stor tykkelse og behovet for å sveise den inn i et ferdig skrog.
Alle som er interessert er sannsynligvis allerede klar over problemene forårsaket av sveising av T -34 rustningen - det er stor sannsynlighet for sprekker i sveisearealet. IS-2 var intet unntak. Og kroppen skulle opprinnelig tilberedes fra endelig varmebehandlede deler.
Etter å ha innsett hvilke vanskeligheter og farer en slik teknologisk løsning ville bringe i militær operasjon, endret TsNII-48-spesialister tankproduksjonssyklusen. Som et resultat, i 1943, ved Ural Heavy Machine Building Plant og Chelyabinsk-anlegget nr. 200, ble IS-2-skroget bestemt for å bli tilberedt av rustningsplater som bare hadde passert en høy ferie etter rulling. Det vil si at skroget til en tung tank var satt sammen av "rått" stål. Dette reduserte sveisefeil sterkt på 51C rullet rustning med høy hardhet.
Den endelige varmebehandlingen ved oppvarming før slukking ble allerede utført på tankens sveisede kropp, etter å ha styrket den med indre stivere. Kroppen ble holdt i ovnen i tre timer. Og så, på spesielle enheter, ble de overført til en vannskjølende tank og oppbevart i den i 15 minutter. Videre steg vanntemperaturen i slukkebeholderen fra 30 til 55 ° C. Overflatetemperaturen til kroppen etter å ha blitt fjernet fra vannet var 100-150 ° С. Og det er ikke alt.
Etter slukking ble kroppen umiddelbart utsatt for lavt temperering i en sirkulerende ovn ved en temperatur på 280-320 ° С med ventetid etter å ha nådd denne temperaturen i 10-12 timer. Lavt temperering av støpte tårn fra 70L rustning ble utført på en lignende måte. Interessant nok var det sprekkkontroll i de eksperimentelle IS-2-skrogene som varte i fire måneder, da de første produksjonstankene forlot fabrikkportene.
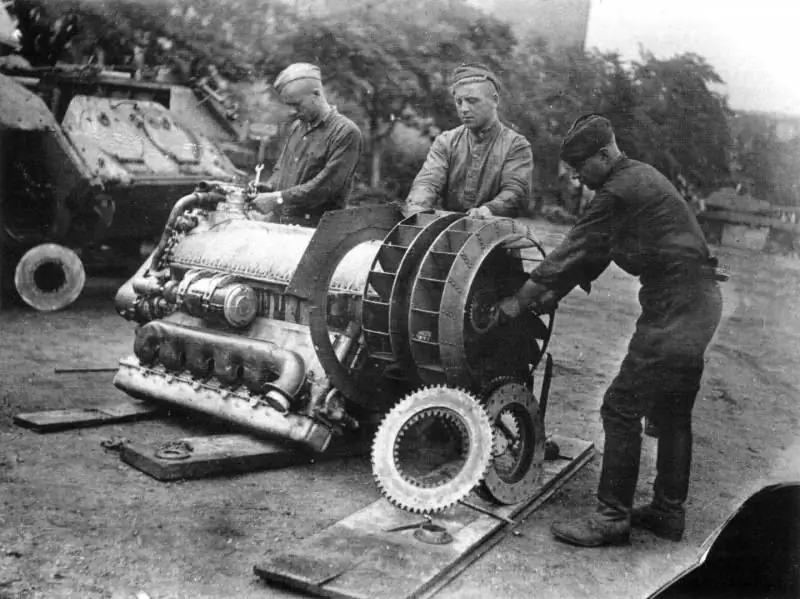
Kjemisk oppbygning
Hva var den 51C rullede rustningen som ble den viktigste for IS-2, ISU-122 og ISU-152? Det er et dypherdende stål for store rustningstykkelser med følgende kjemiske sammensetning (%):
C 0, 18-0, 24
Mn 0, 70-1, 0
Si 1, 20-1, 60
Cr 1, 0-1, 5
Ni 3,0-3,8
Mo 0, 20-0, 40
P ≤ 0,035
S ≤0,035.
I sammenligning med støpt rustning 70L hadde 51C valset stål en høyere andel molybden og nikkel, noe som garanterte en økning i herdbarhet opp til 200 mm. Da skrogene på tunge tanker ble avfyrt med 88 mm skall, viste det seg at rustningen med høy hardhet var langt bedre i holdbarhet enn forgjengerne mellom middels hardhet. Spørsmålet om å plassere rullet rustning 51C ble løst umiddelbart.
Smart sveising
Et viktig bidrag til suksessen med utviklingen av rustningsproduksjon av stridsvogner i IS -serien ble gjort ved automatisk sveising av stål under et flusslag. Siden det var umulig å overføre hele prosessen med å produsere et tankpansret skrog til slik sveising i begynnelsen av 1944, fokuserte ingeniørene på å automatisere de mest forlengede og mekanisk belastede sømmer.
Ved fabrikken i Chelyabinsk nr. 200, under monteringen av skroget til IS-2-tungtanken, kunne bare 25% av alle sveisene automatiseres. I midten av 1944 var Tankograd i stand til å automatisere 18% av alle mulige 25% av sveisene. Den totale lengden på de sveisede sømmene langs skroget på IS-2 tungtank var 410 løpemeter, hvorav 80 løpemeter ble utført med den automatiserte sveisemetoden.
Dette resultatet har ført til betydelige besparelser i knappe ressurser og elektrisitet. Det var mulig å frigjøre opptil 50 kvalifiserte manuelle sveisere (deres lønnskostnader i mengden 15 400 arbeidstimer) og spare 48 000 kilowattimer strøm. Redusert forbruk av elektroder (ca. 20.000 kg, austenittisk - 6000 kg), oksygen (med 1.440 kubikkmeter).
Tiden som brukes på sveising har også blitt betydelig redusert. For eksempel, sveising av bunnen og tårnboksen til sidene med en seksten meter søm tok 9,5 timetimer i manuell modus, og bare 2. En søm med lignende lengde som forbinder bunnen til sidene av tankskroget i automatisk modus kreves 3 arbeidstimer (i manuell umiddelbart 11, 4). Samtidig kan svært dyktige sveisere erstattes av ufaglærte arbeidere innen automatisk sveising.
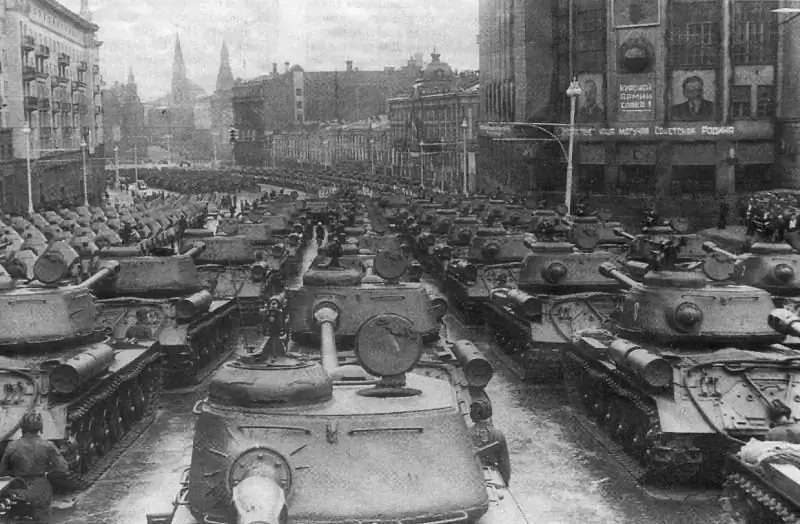
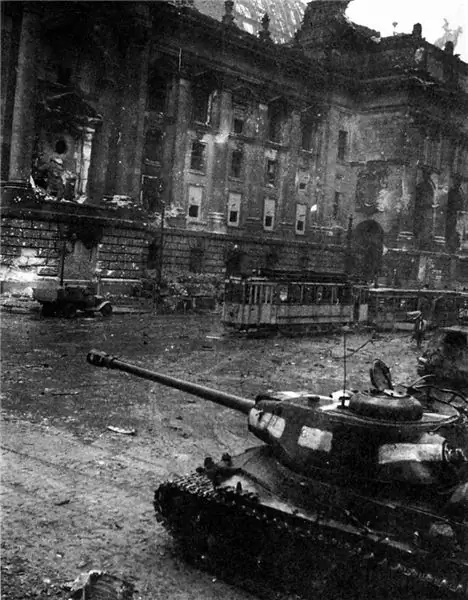
Ural SAG
Forsker for den sovjetiske tankindustrien, kandidat for historiske vitenskaper Zapariy Vasily Vladimirovich fra Institute of History and Archaeology ved Ural Branch of the Russian Academy of Sciences i et av hans arbeider beskriver i stor detalj de automatiske sveiseenhetene som ble brukt i Ural for pansrede skrogproduksjon.
Det mest utbredte var et angrepsgevær av typen "ACC" med et Bushtedt -hode. Det var åtte slike installasjoner på Uralmash. Trådmatingshastigheten i denne maskinen var avhengig av spenningen i buen. Det krevde 5 enheter, inkludert 3 kinematiske elektriske motorer og 1 motorgenerator.
I midten av 1943 ble sveisemaskinen SA-1000 designet for behovene til IS-2 tunge tanker. Eller en sveisemaskin med en kapasitet på opptil 1000 A.
For å mestre produksjonen av pansrede skrog til den nye Tsjelyabinsk tunge tanken IS-3, konstruerte ingeniørene på anlegget i 1944 apparatet "SG-2000". Denne maskinen ble designet for å fungere med sveisetråder med lavt karbonlager med en økt diameter (6-8 mm) og fant sin anvendelse i produksjonen av IS-3-tårnet. Installasjonen hadde en dispenser for innføring av en spesiell sammensetning (forskjellige ferrolegeringer) i sveiseseksjonen for å deoksidere (gjenopprette) metallet i den. Totalt, etter prinsippet om selvregulering av sveisebuen ved UZTM, ble det i 1945 opprettet 9 autosveiseanlegg av tre typer: "SA-1000", "SG-2000", "SAG" ("Automatisk sveising hode").
Mer vakker enn tysk rustning
Resultatet av hele historien med rustningen til tunge IS -tanker var en overraskende rask utvikling av en ståloppskrift som overgikk tysk rustning i sine taktiske egenskaper. TsNII-48 mottok et herdbart 120 mm stål, hvis tykkelse om nødvendig kan økes til 200 mm.
Dette ble hovedgrunnlaget for utviklingen av etterkrigsfamilien med tunge sovjetiske stridsvogner.