Patriotisme til den sovjetiske industrieliten ble kombinert med et felles ansvar for sluttresultatet
Interaksjon mellom industrien til enhver tid - både i det russiske imperiet og i Sovjetunionen, og i dag - tilhørte ikke den innenlandske industriens styrker. I motsetning til Tyskland eller USA, der kontraktsforpliktelser hadde og har en uforanderlig og nesten hellig kraft.
Ta for eksempel forholdet mellom russiske metallurger og maskinbyggere. I andre halvdel av 1800 -tallet mottok nye transporttekniske anlegg og verft ikke den nødvendige mengden industrimetaller fra Ural gruvearbeidere. Sistnevnte anså det som ulønnsomt å lage mange relativt billige valsede produkter, siden det samme overskuddet ble gitt av et mye mindre volum av dyrt takjern. Det manglende metallet til bilaksler, motoraksler og skipskinn måtte kjøpes i utlandet. Først på slutten av århundret ble problemet løst av de sør -russiske metallurgiske anleggene, grunnlagt av belgiske eller franske industrimenn. I Ural bygde franskmennene også et anlegg - Chusovskaya.
Det ser ut til at slike innfall var uaktuelle i sovjetiske tider. I tillegg ga metallurgiske anlegg som ble bygget på 30 -tallet, metallet som helhet. Men hver gang maskinbyggere ba om nye komplekse typer valsede produkter, mestret metallurgene dem i årevis eller til og med tiår.
Avdelingens føydalisme
La oss gå til historien til Uralvagonzavod. Allerede i de første prosjektene var det planlagt å bruke solidvalsede stålhjul under de fire-akslede bilene da designkapasiteten nådde sin designkapasitet, hvis leverandør var planlagt til det nærliggende Novo-Tagil Metallurgical Plant. Imidlertid ble sistnevnte bygget av metallurgisk avdeling, og det utsatte byggingen av hjulvalseverket til 1938-1942, og ikke i utgangspunktet. Som et resultat startet saken ikke før krigen. Og etter krigen var utleie av hjul ikke særlig interessert i metallurger. Resultat: fram til midten av 50-årene forlot Tagil-biler fabrikken på kortvarige støpejernshjul i stedet for stål. Dette medførte store tap for jernbanearbeiderne, men det var ikke noe valg: enten slike biler eller ingen.
Det samme skjedde med introduksjonen av lavlegerte stål i vognbygningen. De lovet en merkbar reduksjon i egenvekten til det rullende materiellet samtidig som de opprettholdt alle ytelsesegenskapene. Designerne av Uralvagonzavod begynte å designe biler laget av lavlegeret metall på slutten av 30-tallet, men serieproduksjonen begynte først i andre halvdel av 50-årene, siden metallurger ikke leverte verken passende valsede produkter eller ferrolegeringer for støping av deler.
Det må sies at viruset av avdelingens føydalisme påvirket maskinbyggerne selv. Sommeren 1937 fant det sted en interessant historie som preget datidens forhold mellom myndigheter. Hoveddirektoratet for metallurgiske selskaper sendte en ordre på fem tusen tonn emner til Uralvagonzavod for det nylig lanserte bandasjefabrikken i Novo-Tagil-anlegget. Hoveddirektoratet for transportteknikk ble rasende over inngrep i et underordnet foretak. Visesjef for hoveddirektoratet G. G.11. juli sendte Aleksandrov et brev til GUMP og Uralvagonzavod med følgende uttalelse: “Vi er ekstremt overrasket over at løsningen på et så viktig problem som å organisere produksjonen av et bandasjemateriale på Uralvagonzavod ble utført uten vår deltakelse, og enda mer - vi ble ikke engang sendt en kopi av antrekket sendt til Uralvagonzavod … Jeg ber deg om å etablere en fast prosedyre for å utstede emner til våre fabrikker bare etter avtale med oss og gjennom Glavtransmash."
Som et resultat ble metallurgene nektet bandasjestålet, angivelig på grunn av den tekniske umuligheten av å støpe høykvalitets barrer i butikken med åpen ild i Uralvagonzavod. I mellomtiden, allerede i 1936, ble det støpt et aksialt emne her, og i 1937 - staver for arkrulling. Derfor måtte ingots for lindemølle, som ligger noen kilometer fra UVZ, transporteres fra Vyksa og Kuznetsk -anleggene. Dessuten forlot kvaliteten mye å være ønsket, og mengden forsyninger var utilstrekkelig.
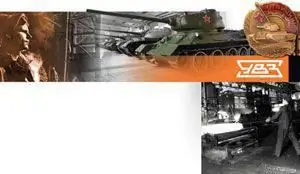
I 1938 gjentok historien seg. Hovedforbrukeren av UVZ -ingots var Molotov (det vil si Perm) Artillery Plant, som mottok et parti emner på slutten av året. Og bare et lite antall av dem dro til bandasjebutikken, som igjen måtte importere det manglende metallet for to eller to og et halvt tusen kilometer. Bransjens interesser i distribusjonen av Uralvagonzavodsk stål seiret tydelig.
Avdelingssykdom sparte ikke forsvarsindustrien heller. Mange publikasjoner om historien til sovjetisk tankbygging er rett og slett fulle av eksempler på hvordan konstruksjonen av prototyper eller distribusjon av masseproduksjon ble forsinket på grunn av manglende levering av metall, spesielt rustning.
Og selv i dag har den sektorielle egeninteressen ikke gått noen steder, den har bare endret form. Forespørsler om nye formede former for valsede produkter bekjempes ganske enkelt med ublu priser. Det er ikke nødvendig å snakke om en samordnet politikk. Etter kollapsen i rubelkursen ved årsskiftet 2014-2015, økte metallurgiske selskaper prisene på rullende materiell med 30-60 prosent. Og de begynte umiddelbart å klage på maskinbyggerne for utstyret som hadde steget i pris - tross alt er maskinene produsert i Russland og er ikke knyttet til dollarkursen.
Det ser ut til at det i vårt land bare er en kur for tverrsektorielle problemer: opprettelsen av vertikalt integrerte systemer, hvor malmen som brytes av våre egne styrker først blir til metall og deretter til ferdige maskiner.
Enhet fra krigen
Det er imidlertid en kort periode i vår historie når bransjens interesser har trukket seg tilbake i bakgrunnen. Vi snakker om den store patriotiske krigen. Den utvilsomme patriotismen til den sovjetiske industrieliten på den tiden ble kombinert med felles ansvar for alle som var involvert i forsvarsproduksjonen for sluttresultatet. Det vil si at direktøren for det pansrede valseanlegget ikke var så mye ansvarlig for volumet av smeltet og valset stål, men for antall tanker som ble bygget.
Hovedtrinnet i denne retningen ble gjort av direktøren for NII-48 A. S. Zavyalov. I de første dagene av krigen vendte han seg til regjeringen med et forslag om å instruere instituttet om å introdusere teknologier for produksjon av spesialstål og pansrede strukturer ved foretak i øst i landet, som først var involvert i produksjon av pansrede kjøretøyer. I begynnelsen av juli ledet team av spesialister fra NII-48 den teknologiske restruktureringen av 14 største virksomheter. Blant dem var Magnitogorsk og Kuznetsk Metallurgical Plants, Novo-Tagil og Chusovka Metallurgical Plants, Ural Heavy Machine Building Plant, Gorky Krasnoye Sormovo, Stalingrad Tractor Plant, Stalingrad Red October og nr. 264. Dermed krenket Zavyalov tabu før krigen: listen inkluderte foretak av tre personers kommisjonærer.
Patriotisme og obligatorisk undertrykkelse av avdelingens egoisme ga sovjetisk metallurgi utviklingshastigheter av forsvarsprodukter uten sidestykke, verken før krigen eller i etterkrigstiden. I løpet av noen måneder, øst i landet (først og fremst i Ural), ble produksjonen av ferromangan, ferrosilisium, ferrokrom, ferrovanadium og andre legeringer organisert, uten hvilken det er umulig å skaffe rustningsstål. Etter tapet av de vestlige regionene forble Chelyabinsk det eneste ferrolegeringsanlegget i Sovjetunionen. På den, på kort tid, ble smeltingen økt med to og en halv gang. Det ble produsert 25 typer produkter, men mest av alt var det forskjellige typer ferrokrom. Smelting av ferromangan ble etablert i masovner, og ikke bare i gamle masovner med lav tonnasje fra Nizhniy Tagil- og Kushvinsky-anleggene, men også i en stor moderne ovn i Magnitogorsk Combine. I motsetning til alle førkrigstidens ideer ble ferrokrom smeltet i andre halvdel av 1941 i masovnene av metallurger fra Nizhniy Tagil- og Serov-anleggene, og forskere fra Ural-grenen av USSR Academy of Sciences ga stor hjelp til å lage et nytt teknologi. Senere ble ferrosilisiumsmelting mestret i høyovnene i Serov.
Det var ingen pansrede leire verken i Ural eller i Vest -Sibir før krigen, de måtte hastig overføres fra foretak som var i kampsonen.
Sommeren 1941 var det evakuerte utstyret fortsatt i transitt. Og så foreslo hovedmekanikeren i Magnitogorsk Combine N. A. Ryzhenko å rulle rustningen på en blomstrende mølle. Til tross for den store risikoen, ble ideen gjennomført. Og i oktober gikk en pansret leir, hentet fra Mariupol -anlegget, i tjeneste. Den ble satt sammen på bare 54 dager. I henhold til førkrigsstandardene tok dette et år.
Novo-Tagil-anlegget fikk leiren fra Leningrad. Forberedelsene til opptaket begynte i juli, først ble det antatt at det ville bli montert på stedet for bandasjen. Bandasjeleiren ble demontert, men det viste seg at den gamle bestanden ikke var nok til å installere den pansrede leiren og måtte plasseres andre steder. Krigen tvunget til å gjøre det som ble ansett som umulig inntil nylig: For bare et år siden hadde forsøk på å utføre industriell konstruksjon ved en integrert "høyhastighets" metode i Nizhny Tagil i beste fall delvis suksess, og sommeren 1941 var det mest kompleks konstruksjonsoperasjon var nesten perfekt. September ble det første Tagil -stålplaten rullet en måned før planen. Totalt ble det ved utgangen av året oppnådd 13 650 tonn metallplater, inkludert om lag 60 prosent rustning (møllen ble testet på karbonstål, og i oktober - desember ble karbonstål rullet med mangel på rustningsblokker). Som et resultat, allerede i januar 1942, oversteg den månedlige produksjonen av rustningsplater ved Ural-fabrikkene seks måneder i hele Sovjetunionen før krigen.
Ikke mindre overraskende hendelser fant sted på andre lite kjente virksomheter. Under krigen var Zlatoust Metallurgical Plant dårligere enn Magnitogorsk -skurtreskeren når det gjelder volumet av smelting og valset stål, men det overgikk det betydelig i sin produktmiks - rundt 300 legeringer og karbonstål ble produsert her. Uten forsyninger fra Zlatoust ville produksjonen av mange typer våpen, først og fremst tankmotorer, ha stoppet.
Gamle Ural-fabrikker viste seg å være uunnværlige i produksjonen av små partier av stål av spesielt høy kvalitet. For eksempel ble metall fra Serov Metallurgical, hovedprodusenten av kalibrerte valsede produkter, investert i hver sovjetisk tank. Nizhnesalda -anlegget gikk over til nikkeljern og stålsmelting. Denne listen kan videreføres uendelig - i krigsårene, hvor det var minst en kuppel, ble metall av våpenklasse smeltet.
Det er en nysgjerrig historie med flukser for automatisk sveising. Før og i begynnelsen av krigen ble de smeltet på et av Donbass -foretakene, etter at okkupasjonen som sentraliserte forsyninger fullstendig stoppet. På slutten av 1941 begynte ansatte ved Institute of Electric Welding of the Academy of Sciences i den ukrainske SSR å lete etter substituttmateriale tilgjengelig i Ural i en mer eller mindre brukbar tilstand. Og de fant dem - i form av masovnslagger fra Ashinskiy metallurgiske anlegg. Bare små forbedringer var nødvendig: Masovnene beriket slaggene sine med mangan og gjorde dem derved til en helt passende fluks. Utstyret som er nødvendig for testing ble brakt fra Nizhny Tagil direkte til Asha.
Eksempler på lokalt samarbeid mellom tank- og metallurgiske anlegg er veldig veiledende. Før lanseringen av egne anlegg, ble varmebehandling av tankdeler av Ural tankanlegg nr. 183 utført ved Nizhniy Tagil metallurgiske anlegg.
Det vellykkede arbeidet til UTZ støperiarbeidere ble sterkt tilrettelagt av bistand fra det nærliggende Nizhniy Tagil brannsteinanlegget, som etablerte produksjonen av ildfaste stoppflintplugger av høy kvalitet. Dette gjorde det mulig å utføre problemfri støping av tungt rustningsstålsmelt for formstøping.
I 1942-1945 drev åpne ovner ved UTZ hovedsakelig koksovn og masovngass fra Novo-Tagil Metallurgical og Nizhniy Tagil Coke Plants. Gassledningen har vært i drift siden februar 1942. Anlegg nr. 183 egen gassterminal ga ikke mer enn 40 prosent av behovene.
Noen ganger var et enkelt råd nok til å løse et problem. Informasjonen fra lokale metallurger om en liten mangangruve utviklet på 1870 -tallet bidro til å overleve flere uker før starten av leveranser av ferromanganer uten å stoppe støping av tankspor.
Et annet eksempel: etter hvert som produksjonen av pansret stål økte, kunne butikken med åpen ild ikke lenger følge med smeltingen av metall for hodene på flybomber. Det var ikke mulig å få det utenfra. Direktør Yu. E. Maksarev husket forløpet til ytterligere hendelser i memoarene: “Da jeg var på et av møtene i bykomiteen, møtte jeg direktøren for det gamle, fortsatt Demidov -anlegget og ba om å ta fra meg støpingen av bombehodene. Han sa: Jeg kan ikke hjelpe med stål, men med råd vil jeg hjelpe. Og da jeg kom til anlegget hans, viste han meg en og et halvt tonn Bessemer -omformer med middels blåsing. Han ga meg tegningene og sa at han vet at vi har et godt mekanisert jernstøperi, og omformerne dine vil sveise”. Slik fremkom ordren for anlegget 8. september 1942 på organisasjonen i Griffin -hjulbutikken i Bessemer -delen av tre små omformere (halvannet tonn metall hver). Senest 25. september ble prosjektet utarbeidet av design- og teknologisk avdeling for hovedbygningsledelsen, spesialistene på hovedmekanikkavdelingen sveiset raskt omformere og kjeler - lagertanker for flytende jern. Testkjøringen til Bessemer-avdelingen og støping av et eksperimentelt parti med fem navn på deler fant sted i begynnelsen av oktober-november 1942. Seriell produksjon begynte i slutten av november.
På slutten av emnet: samarbeidet mellom metallurger og tankbyggere i krigstid virket i begge retninger. Installatørene av Ural Tank Plant deltok i igangkjøring av mange nye enheter på Novo-Tagil Metallurgical Plant. I mai 1944 ble et betydelig antall foringsplater for reparasjon av masovnen produsert i det pansrede tårnstøperiet.
Men hovedassistenten til metallurgene var selvfølgelig Ural Heavy Machine Building Plant. Ordrebøkene for UZTM for 1942-1945 er bokstavelig talt fullpakket med dokumenter om produksjon av reservedeler og enheter til metallurgiske formål - både for tankindustriens behov og for foretakene til People's Commissariat of Ferrous Metallurgy. Høsten 1942 ble en spesiell avdeling for produksjon av utstyr til metallurgiske anlegg offisielt restaurert ved UZTM. Den mottok koden "Divisjon 15" og var underordnet visedirektøren for innkjøpsbutikker og skrogproduksjon.
Suksess i krysset mellom næringer
Samarbeidet mellom metallurger og tankbyggere har ført til etableringen av en rekke teknologier som uten overdrivelse kan kalles reelle vitenskapelige og tekniske gjennombrudd.
Etter å ha smeltet og rullet rustningstål til plater, overførte metallurgene produktene sine til pansret skrogproduksjon. Her ble metallet skåret i henhold til malen i de tilsvarende delene. I produksjonen av "tretti-fire" ble spesielt mye trøbbel levert av to deler av skroget: skjerm (skrå side av siden) og den vertikale sideplaten. Begge var lange, selv i breddebånd med skrå snitt langs kantene.
Ideen foreslo selvsagt å rulle en målebånd som var like bred som de ferdige delene. Den ble først formulert av pansrede biler på Mariupol -anlegget sommeren 1941. For prøvevalsing valgte vi et slabbemølle i Zaporizhstal, hvor det ble sendt to lag med rustningsbarrer. Men da hadde de ikke tid til å komme i gang: de fremrykkende tyske troppene fanget både echelons og Zaporozhye selv.
Ved årsskiftet 1941-1942, under evakueringen og utviklingen av rustningsproduksjonen ved de nye fabrikkene, var det ikke nok stripe. Imidlertid mottok People's Commissariat of Ferrous Metallurgy i mai 1942 igjen en ordre om å leie den for T-34 og KV-tanker. Oppgaven viste seg å være vanskelig: toleransene i bredden bør ikke overstige -2/ + 5 millimeter, halvmåneformen (bøyningen) for delens totale lengde var 5 millimeter. Sprekker, solnedganger og delaminering var ikke tillatt i kantene slik at sveising kunne utføres uten maskinering eller flammeskjæring.
Eksperimentelt arbeid begynte samtidig i de rullende butikkene ved metallurgiske fabrikkene i Magnitogorsk og Kuznetsk, først uten spesielle prestasjoner. Leie av deler til KV-tankene ble snart forlatt, men T-34 ble til slutt vellykket. Forfatterteamet som består av lederen for metallurgisk avdeling ved NII-48 G. A. Vinogradov, maskiningeniør for KMK L. E. Vaisberg og ingeniøren for det samme anlegget S. E. står "900" for jernbane- og konstruksjonsfabrikken er en helt ny metode for å rulle "på kanten". I januar 1943 ble 280 strimler utstedt, i februar - 486, i mars - 1636 stykker. I april, etter alle de nødvendige testene, begynte utviklingen av bruttoproduksjonen av målebånd for hjulbuerne på T-34-tanker. I utgangspunktet ble de levert til UZTM og Ural Tank Plant, og deretter til andre fabrikker - produsenter av T -34 -tanker. Skrotet, som opprinnelig var 9,2 prosent, hadde falt til 2,5 prosent i oktober 1943, og de ikke -standardiserte stripene ble brukt til å lage mindre deler.
En fullstendig og nøyaktig vurdering av den nye teknologien er gitt av den tilsvarende rapporten fra TsNII-48 datert 25. desember 1943: "En grunnleggende ny metode for å rulle en bred pansret stripe" på kanten "ble utviklet, testet og introdusert i bruttoproduksjon, som ble ansett som uoppnåelig inntil nylig i Sovjetunionen og i utlandet. Å skaffe en kalibrert (målt) stripe med bredden på den ferdige delen av det pansrede skroget på T-34-tanken gjorde det mulig for NKTP-fabrikkene å ta i bruk en ny høyytelsesteknologi for produksjon av pansrede deler uten å kutte langsgående kanter. Takket være anvendelsen av den nye metoden på en av de viktigste pansrede delene av T-34-tanken (fendere), ble det oppnådd en meget betydelig tidsbesparelse (ca. 36%) når de ble kuttet ut. Oppnådde besparelser på 8C rustningstål opp til 15 prosent og oksygenbesparelser på 15 000 cbm per 1000 skrog”.
I slutten av 1943 ble rulling av en målebånd mestret for en annen del av T -34 -skroget - den vertikale delen av siden. Det gjenstår bare å legge til at forfatterne av denne oppfinnelsen ble tildelt Stalinprisen for 1943.
I samme 1943, ved felles innsats fra laboratoriet til det ukrainske metallinstituttet (ledet av PA Aleksandrov) og arbeidere ved Kuznetsk Metallurgical Combine og Ural Tank Plant, ble en spesiell periodisk rullet profil utviklet og mestret i produksjon for anskaffelsen av masse og kritiske deler av de "tretti -fire" - balanse -aksene. Den første eksperimentelle batchen av en periodisk profil ble mottatt på KMK i desember, i begynnelsen av 1944 begynte serieproduksjonen. I oktober byttet Ural tankanlegg helt til produksjon av balanseaksler fra et nytt emne, på slutten av året ble UZTM med. Som et resultat økte produktiviteten til smiehammerne med 63 prosent og antall brudd på deler redusert.
Tankbyggernes vellykkede arbeid ble sterkt lettere av det rullende materiellet til bandasjefabrikken i Novo-Tagil Metallurgical Plant. Fra og med våren 1942 leverte de rullede skulderstropper med redusert bearbeidingstillatelse, i 1943 ble kvotene redusert igjen. I kombinasjon med det nye skjæreverktøyet gjorde dette det mulig å gjennomføre tidkrevende stripping av skulderstropper strengt etter planen og uten mye stress. Et sjeldent tilfelle: Folkekommissæren for tankindustrien V. A. Malyshev anså i sin ordre 28. september 1943 det nødvendig å uttrykke spesiell takknemlighet overfor metallene i Tagil.
Og til slutt, det siste eksemplet: I 1943 begynte felgene til T-34-støttetankene, først ved Chelyabinsk Kirov-anlegget, og deretter på andre foretak, å være laget av spesialprofilerte valsede produkter. Denne suksessen ble også notert i rekkefølgen av V. A. Malyshev.
Det gjenstår å legge til at spesialistene til det amerikanske selskapet "Chrysler", etter å ha studert tanken T-34-85 fanget i Korea, spesielt bemerket perfeksjonen til stålemnene som kampvognen ble laget av. Og også det faktum at de ofte var flere enn produktene fra de amerikanske metallurgiske foretakene.